What basic governor troubles are apt to occur? Answers: Hunting-alternate speeding and slowing of the engine, which means that the governor is too sensitive to load changes. Sticking-failure to control speed, allowing the engine to run away or slow down-which means that the governor is not sensitive to load changes or parts are binding or worn. What is a governor safety stop? Answers: On throttling-type governors, the safety stop is a weighted arm that needs the support of a governor belt. If the belt breaks, the idler arm drops and shuts the steam supply valve to the engine. On Corliss units, the flyballs fall to the lowest position and knock off the safety cams; the cams disengage the catch blocks on the steam intake valves so that no steam is admitted to the engine.
Why is condensation or excessive carryover dangerous to reciprocating engines? Answer: Because water is non-compressible. If an excessive amount of water gets into the cylinder, it will wreck the engine.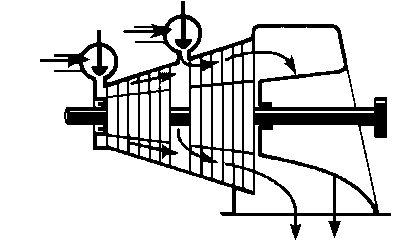
Why should a steam or moisture separator be installed in the steam line next to a steam turbine? Answer: All multistage turbines, low-pressure turbines, and turbines operating at high pressure with saturated steam should have a moisture separator in order to prevent rapid blade wear from water erosion. Under what conditions may a relief valve not be required on the exhaust end of a turbine? Answer: If the manufacturer has provided that the turbine shells are constructed for full-inlet steam pressure for the entire length of the shell. It is absolutely essential to have a relief valve to protect the shell in the event an exhaust valve is closed and high-pressure steam is admitted to the shell on the front end of the machine. Explosions have occurred when this happened.
What are some conditions that may prevent a turbine from developing full power? Answers: The machine is overloaded. The initial steam pressure and temperature are not up to design conditions. The exhaust pressure is too high. The governor is set too low. The steam strainer is clogged. Turbine nozzles are clogged with deposits. Internal wear on nozzles and blades.
Why is it necessary to open casing drains and drains on the steam line going to the turbine when a turbine is to be started?. Answers: To avoid slugging nozzles and blades inside the turbine with condensate on start-up; this can break these components from impact. The blades were designed to handle steam, not water.
What three methods are used to restore casing surfaces that are excessively eroded? Answers: Metal-spraying. Welding. Insertion of filler strips or patch plates. The manufacturer should be consulted on the metallurgy involved so that the best method can be selected.
What is steam rate as applied to turbo-generators? Answer: The steam rate is the pounds of steam that must be supplied per kilowatt-hour of generator output at the steam turbine inlet.
What is the most prevalent source of water induction into a steam turbo-generator? Answer: Leaking water tubes in feedwater heaters, which have steam on the shell side supplied from turbine extraction lines. The water at higher pressure can flow back into the turbine because the extraction steam is at a lower pressure. Check valves are needed on the steam extraction line to prevent the back-flow of water into the turbine.
What is a regenerative cycle? Answer: In the regenerative cycle, feedwater is passed through a series of feed-water heaters and is heated by steam extracted from stages of a steam turbine. This raises the feedwater to near the temperature of boiler water, thus increasing the thermal efficiency of the cycle. What is the re-heating cycle? Answer: In the re-heating cycle, superheated steam is expanded in a high-pressure turbine and then returned to the boiler's re-heater to raise the temperature of the steam to the inlet temperature, usually to around 537°C; it is then returned to the turbine to be expanded through intermediate-pressure turbines. In some cases, the steam is again returned for re-heating in the boiler and then expanded in the lower- pressure sections of the turbine. The main purpose of re-heating the steam on large turbo-generators is to avoid condensation in the lower- pressure sections of the turbine, which can rapidly cause blade erosion problems from wet steam. What does the Willans line show? Answer: The Willians line is a plot of throttle flow versus the load, usually expressed in kilowatts; generally it is a straight line except for low and high loads. The Willians line is used to show steam rates at different loads on the turbine.
What are topping and superposed turbines? Answer: Topping and superposed turbines arc high-pressure, non-condensing units that can be added to an older, moderate-pressure plant. Topping turbines receive high-pressure steam from new high-pressure boilers. The exhaust steam of the new turbine has the same pressure as the old boilers and is used to supply the old turbines. What is an extraction turbine? Answer: In an extraction turbine, steam is withdrawn from one or more stages, at one or more pressures, for heating, plant process, or feedwater heater needs. They are often called "bleeder turbines." What are four types of thrust hearings? Answer: Babbitt-faced collar bearings. Tilting pivotal pads. Tapered land bearings. Rolling-contact (roller or ball) bearings. What is the function of a thrust bearing? Answer: Thrust bearings keep the rotor in its correct axial position. What is a balance piston? Answer: Reaction turbines have axial thrust because pressure on the entering side is greater than pressure on the leaving side of each stage. To counteract this force, steam is admitted to a dummy (balance) piston chamber at the low-pressure end of the rotor. Some designers also use a balance piston on impulse turbines that have a high thrust. Instead of piston, seal strips are also used to duplicate a piston's counter force. What is a combination thrust and radial bearing? Answer: This unit has the ends of the babbitt bearing extended radially over the end of the shell. Collars on the rotor face these thrust pads, and the journal is supported in the bearing between the thrust collars.
What is a tapered-land thrust bearing? Answer: The babbitt face of a tapered-land thrust bearing has a series of fixed pads divided by radial slots. The leading edge of each sector is tapered, allowing an oil wedge to build up and carry the thrust between the collar and pad.
What is important to remember about radial bearings? Answer: A turbine rotor is supported by two radial bearings, one on each end of the steam cylinder. These bearings must be accurately aligned to maintain the close clearance between the shaft and the shaft seals, and between the rotor and the casing. If excessive bearing wear lowers the he rotor, great harm can be done to the turbine.
What is gland-sealing steam? Answer: It is the low-pressure steam that is led to a sealing gland. The steam seals the gland, which may be either a carbon ring or labyrinth type against air at the vacuum end of the shaft.
What is the function of a gland drain? Answer: The function of a gland drain is to draw of water from sealing-gland cavities created by the condensation of sealing steam.
What is an air ejector? Answer: An air ejector is a steam siphon that removes non-condensable gases from the condenser.
How many governors are needed for safe turbine operation? Why? Answer: Two independent governors are needed for safe turbine operation. One is an overspeed or emergency trip that shuts off the steam at 10 percent above running speed (maximum speed). The second, or main governor, usually controls speed at a constant rate; however, many applications have variable speed control.
How is a flyball governor used with a hydraulic control? Answer: As the turbine speeds up, the weights are moved outward by centrifugal force, causing linkage to open a pilot valve that admits and releases oil on either side of a piston or on one side of a spring-loaded piston. The movement of the piston controls the steam valves.
What is a multi-port governor valve? Why is it used? Answer: In large turbines, a valve controls steam flow to groups of nozzles. The number of open valves controls the number of nozzles in use according to the load. A bar-lift or cam arrangement operated by the governor opens and closes these valves in sequence. Such a device is a multi-port valve. Using nozzles at full steam pressure is more efficient than throttling the steam.
What is meant by critical speed? Answer: It is the speed at which the machine vibrates most violently. It is due to many causes, such as imbalance or harmonic vibrations set up by the entire machine. To minimize damage, the turbine should be hurried through the known critical speed as rapidly as possible. (Caution, be sure the vibration is caused by critical speed and not by some other trouble).
How is oil pressure maintained when starting or stopping a medium-sized turbine? Answer: An auxiliary pump is provided to maintain oil pressure. Some auxiliary pumps are turned by a hand crank; others are motor-driven. This pump is used when the integral pump is running too slowly to provide pressure, as when starting or securing a medium-sized turbine.
Why is it poor practice to allow turbine oil to become too cool? Answer: If a turbine oil is allowed to become too cold, condensation of atmospheric moisture takes place in the oil and starts rust on the polished surfaces of the journal bearings. Condensed moisture my interfere with lubrication. Steam blowing from a turbine gland is wasteful.
Why else should it be avoided? Answer: It should be avoided because the steam usually blows into the bearing, destroying the lubrication oil in the main bearing. Steam blowing from a turbine gland also creates condensate, causing undue moisture in plant equipment. Besides lubrication, which are two functions of lubricating oil in some turbines? Answer: In large units, lube oil cools the bearings by carrying off heat to the oil coolers. Lube oil in some turbines also acts as a hydraulic fluid to operate the governor speed-control system.
What is meant by the water rate of a turbine? Answer: It is the amount of water (steam) used by the turbine in pounds per horsepower per hour or kilowatts per hour.
Why is there a relief valve on a turbine casing? Answer: The turbine casing is fitted with spring-loaded relief valves to prevent damage by excessive steam pressure at the low-pressure end if the exhaust valve is closed accidentally. Some casings on smaller turbines are fitted with a sentinel valve, which serves only to warn the operator of over-pressure of the exhaust end. A spring-loaded relic valve is needed to relieve high pressure.
Why must steam turbines be warmed up gradually? Answer: Although it is probable that a turbine can, if its shaft is straight, be started from a cold condition without warming up, such operation does not contribute to continued successful operation of the unit. The temperature strains set up in the casings and rotors by such rapid heating have a harmful effect. The turbine, in larger units especially should be warmed slowly by recommended warm-up ramp rates because of close clearances.
What should you lost vacuum while operating a condensing turbine plant? Answer: If vacuum is lost shut down immediately. The condenser cannot stand steam pressure, the condenser tubes may leak from excessive temperature. Excessive pressure will also damage the shell, the exhaust and the low-pressure parts of the turbine.
What are the main causes of turbine vibration?
Answers: Unbalanced parts. Poor alignment of parts. Loose parts. Rubbing parts. Lubrication troubles. steam troubles. Foundation troubles. Cracked or excessively worn parts. What is the purpose of a turning gear? Answer: Heat must be prevented from warping the rotors of large turbines or high-temperature turbines of 400°C or more. When the turbine is being shut down, a motor-driven turning gear is engaged to the turbine to rotate the spindle and allow uniform cooling. What does he term "ramp" rate mean? Answer: Ramp rate is used in bringing a turbine up to operating temperature and is the degrees Celsius rise per hour that metal surfaces are exposed to when bringing a machine to rated conditions. Manufacturers specify ramp rates or their machines in order to avoid thermal stresses. Thermocouples are used in measuring metal temperatures.
What is the difference between partial and full arc admission? Answer: In multi-valve turbine inlets, partial arc ad mission allows the steam to enter per valve opening in a sequential manner, so as load is increased, more valves open to admit steam. This can cause uneven heating on the high-pressure annulus as the valves are individually opened with load increase. In full-arc admission, all regulating valves open but only at a percentage of their full opening. With load increase, they all open more fully. This provides more uniform heating around the high-pressure part of the turbine. Most modern controls start with full-arc and switch to partial arc to reduce throttling losses through the valves.
What are some common troubles in surface-condenser operation? Answer: The greatest headache to the operator is loss of vacuum caused by air leaking into the surface condenser through the joints or packing glands. Another trouble spot is cooling water leaking into the steam space through the ends of the tubes or through tiny holes in the tubes. The tubes may also become plugged with mud, shells, debris, slime or algae, thus cutting down on the cooling water supply. Corrosion may be uniform, or it may occur in small holes or pits.
Where would you look for a fault if the air ejector didn't raise enough vacuum? Answers: In this case, the trouble is usually in the nozzle. You will probably find that the nozzle is eroded. The strainer protecting the nozzle is clogged. The steam pressure to the nozzle is too low.
|